Strictly according to schedule
Components for car heaters are shipped by sea from Hamburg to Langfang in China. The supply chain must hold firm. Otherwise riding in the car would be uncomfortable—something that Gentherm and DACHSER take a dim view of.
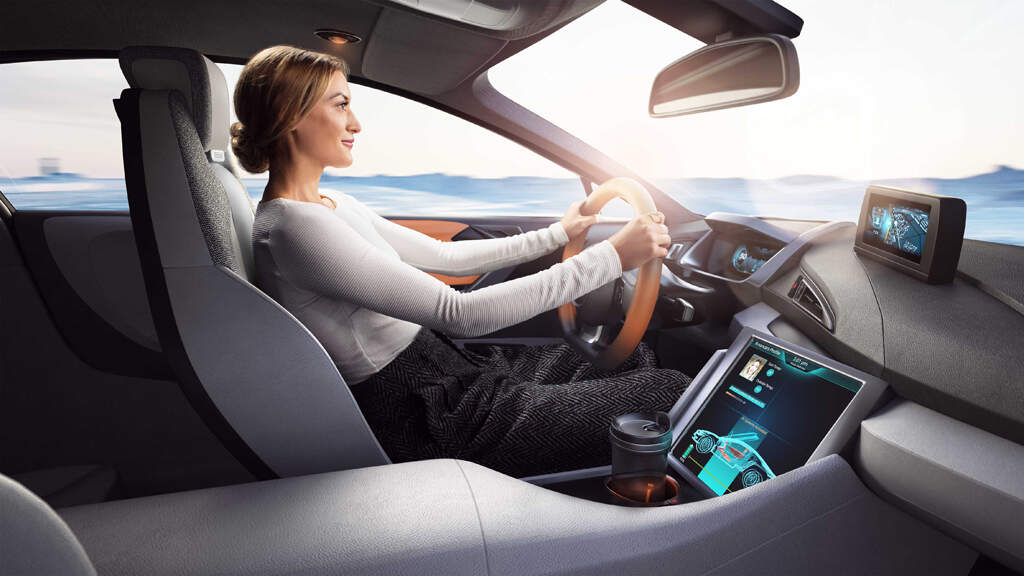
Transporting raw materials is part of day-to-day operations for automotive supplier Gentherm and serves as the basis for its smoothly functioning business. The electronic components, cables, and heated and cooled seats, e.g., for car seats, are shipped via the Road Logistics network from their production sites in Germany, Hungary, the UK, and Ukraine to DACHSER, where they are packaged and transported to the nearest port; Hamburg, for example. There, containers and vessels are waiting to ship them overseas. A frequent destination is Tianjin in China. From the port, the shipment continues on by truck to the Gentherm production facility in Langfang.
The average duration of this sea transport, which is organized and supervised by DACHSER, is 45 days from door to door. This sounds fast, but compared to other routes, it is actually quite long. The journey between Hamburg and Del Rio, Texas is “only” 19 days; it’s 15 days between Langfang and Japan, and 8 days between Hong Kong and Korea.
But when it comes to where his raw materials are at any given moment, Matthew Pisani, Global Transportation Manager at Gentherm, doesn’t want to be involved. That is the job of the service providers, which often includes DACHSER specialists, one of whom is Hubert Diepolder, Key Account Manager of DACHSER Air & Sea Logistics in Munich. Together with their colleagues from DACHSER Road Logistics, he and his team ensure that more than 1,100 shipments per month from Europe alone reach Gentherm’s production facilities across the globe - punctually and in good condition, so that the manufactured cars are always comfortably warm.
The most valuable “currency”: punctuality
If the automotive industry’s closely timed supply chains are late by even just a day, it disrupts the entire supply chain. “We depend on a regular delivery frequency,” says Pisani. Any delay could result in complex production processes grinding to a halt. “That’s something we don’t want under any circumstances,” he explains, as he describes the most important quality he requires from his logistics partner DACHSER.
Wanted: “anticipators” and copilots
And that’s not always easy - especially when something unexpected happens, like shipping giant Hanjin filing for bankruptcy. Or when ports and airports are crippled by strikes or the pilots go on strike. An active crisis management is essential for Matthew Pisani. “That is why we rely on a service provider who is flexible and actively anticipates our requirements. We need a multi-faceted logistics system that can do everything."